
The healthcare sector, one of society's essential pillars, continues to face significant challenges related to its operational efficiency, quality of care, and cost control. These challenges are exacerbated by the increasing demand for healthcare services, technological advancements, and economic pressures.
To address these challenges more effectively, many healthcare organizations are turning to innovative approaches, such as Lean Healthcare. Lean Healthcare is a methodology inspired by the successful practices of the Japanese automotive industry, like the Toyota Production System, aimed at optimizing processes and improving patient care. It is an approach that seeks to eliminate waste, reduce inefficiencies, and enhance the quality of healthcare services.
In this article, learn more about the fundamentals of Lean Healthcare and how this methodology can be practically applied to overcome specific challenges in the healthcare sector.
Before we continue, we need to ask: Are you already familiar with Ninsaúde Clinic? Ninsaúde Clinic is a medical software with an agile and complete schedule, electronic medical records with legal validity, teleconsultation, financial control, health insurance billing, and much more. Schedule a demonstration or try Ninsaúde Clinic right now!

Principles of Lean Healthcare
Lean Healthcare is based on five fundamental principles:
- Identify Value for the Patient: The first step is to understand what is truly valuable to the patient. This involves identifying aspects of healthcare that have a direct impact on the patient's health and satisfaction.
- Value Stream Mapping: After understanding value for the patient, it is crucial to map the entire process of service delivery, from admission to discharge. This helps identify inefficiencies and areas of waste.
- Create Continuous Flow: Lean Healthcare seeks to eliminate disruptions and bottlenecks in processes, promoting a continuous and efficient flow of information, materials, and patients.
- Customer Pull Production: Instead of overproducing and stockpiling, Lean Healthcare adopts a customer pull production approach, where patient demand guides the delivery of services and resource utilization.
- Pursuit of Excellence: Lean Healthcare is an ongoing process of improvement, where teams continually seek excellence by identifying opportunities for enhancement and implementing incremental improvements.
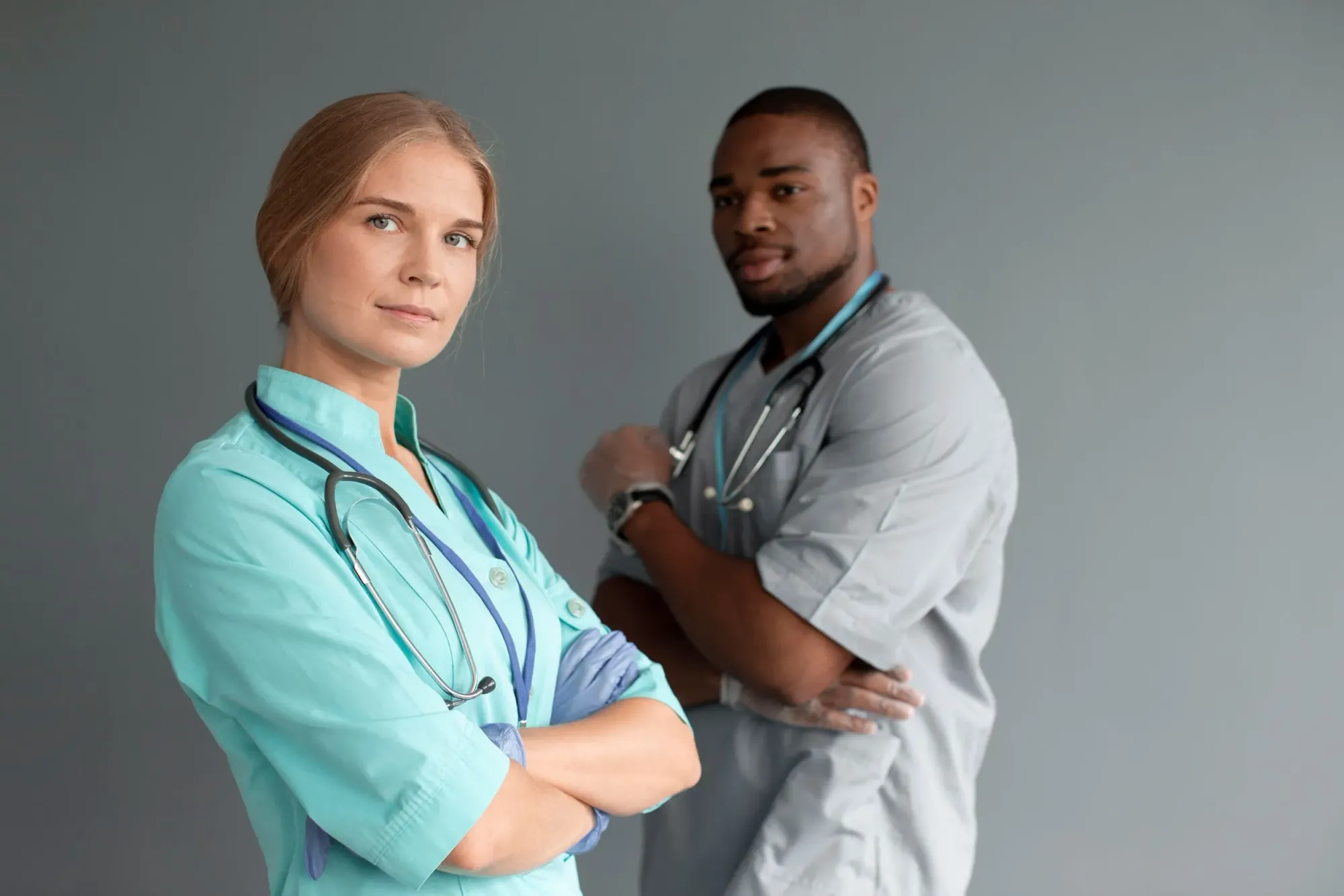
Challenges in Healthcare and Lean Solutions
Wait Times
Challenge: One of the pressing challenges that directly impacts the quality and effectiveness of healthcare services is the issue of long waiting periods faced by patients awaiting medical appointments and procedures. This issue not only compromises the patient's experience but can also have serious implications for people's health and well-being.
Lean Healthcare Solution: In the context of Lean Healthcare, addressing wait times is a top priority. The application of Lean principles in the healthcare sector provides a structured and effective approach to tackle this challenge. The Lean methodology aims to identify and eliminate all activities that do not add value to the patient, including excessive waiting.
One of the most powerful techniques of Lean Healthcare to reduce wait times is the optimization of the patient flow. This involves a detailed analysis of care processes, identifying bottlenecks and constraints, and implementing improvements to ensure a smoother and more efficient flow. Process standardization and proper resource allocation also play a crucial role in reducing wait times.
Furthermore, Lean Healthcare values the voice of the patient by encouraging active participation in the care process. This may involve setting realistic expectations for wait times, transparent communication about the status of care, and a continuous search for ways to make the patient's experience more pleasant, even when inevitable delays occur.
Concrete examples of successful implementation of Lean Healthcare to reduce wait times include the restructuring of appointment schedules, the creation of more efficient workflows in emergency units, and the use of technology to improve communication between patients and healthcare professionals, such as the Ninsaúde Clinic software.
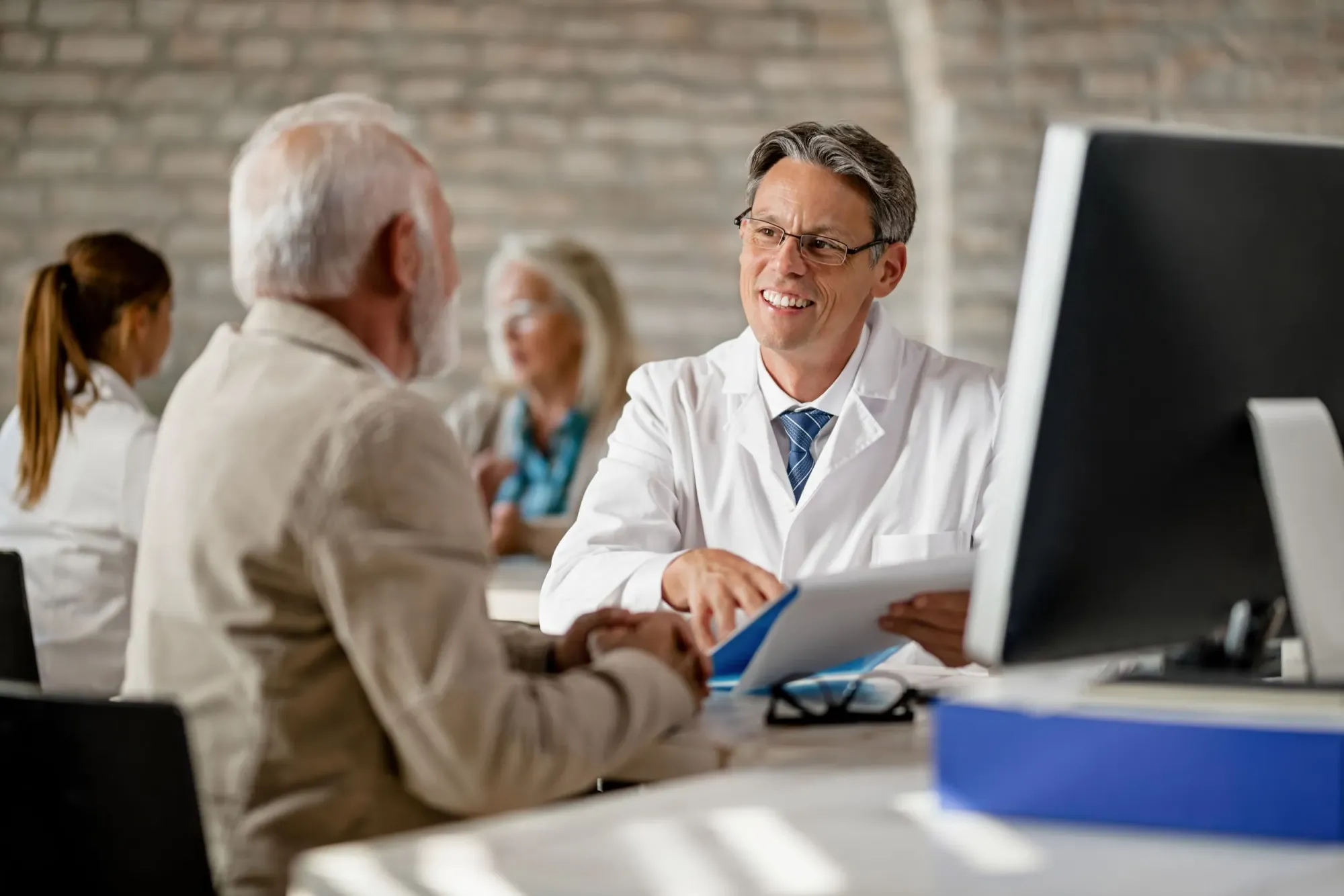
Resource Management
Challenge: The inefficient allocation of human and material resources in the healthcare sector is a complex problem that directly impacts the capacity of care and the quality of services provided. Many healthcare organizations face the challenge of optimizing the utilization of human resources, such as doctors, nurses, and other healthcare professionals, as well as material resources, such as medical equipment and supplies, due to high demand and cost reduction pressure.
Lean Healthcare Solution: In this context, Lean Healthcare methodology plays a crucial role in addressing this challenge. Value stream analysis, one of Lean's key tools, is a systematic approach that helps identify all stages of a process, from the patient's arrival to the delivery of medical services. This includes all interactions, activities, and resources involved in the patient care process.
By mapping the value stream, healthcare organizations can identify redundancies, inefficiencies, and waste throughout the process. This provides a holistic view of operations, highlighting areas where resource allocation can be optimized. For example, value stream analysis may reveal that certain tasks are being performed by highly skilled healthcare professionals when they could be delegated to other team members, freeing up valuable resources for more critical tasks.
A practical example of applying Lean Healthcare to address the challenge of inefficient resource allocation is the review and restructuring of doctors' and nurses' work schedules. By adjusting work schedules based on actual demand and team capacity, healthcare organizations can ensure a more effective allocation of human resources.
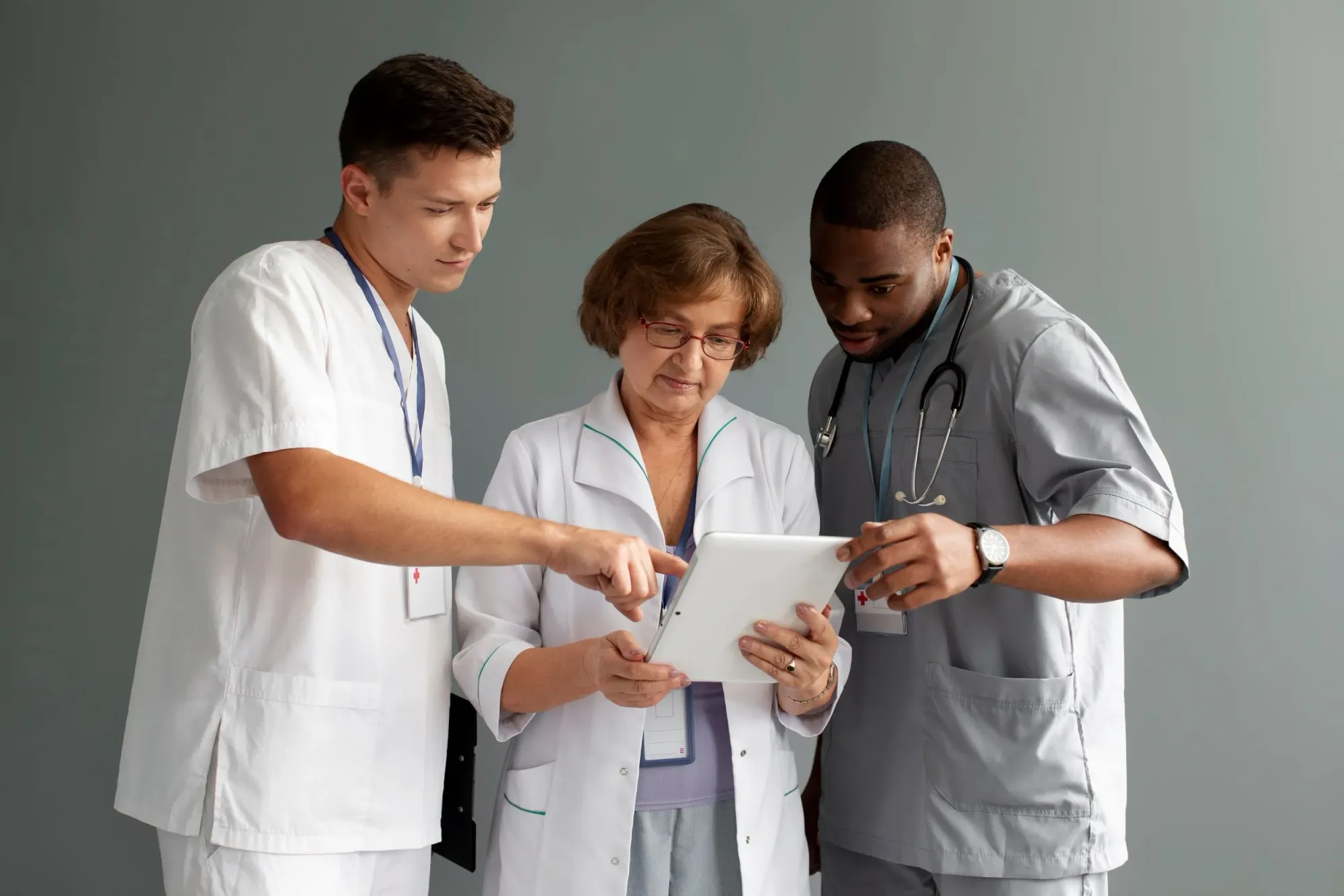
Similarly, value stream analysis can identify underutilized or poorly located medical equipment, allowing for more strategic reallocation to better meet the needs of patients with greater efficiency.
Lack of Patient Engagement
Challenge: A significant challenge in the healthcare sector is the frequent sense of disconnect that patients experience regarding the care process. Often, patients feel passive about their treatment, with few opportunities to influence decisions related to their health. This disconnection can lead to a lack of patient engagement, resulting in a less satisfactory care experience and ultimately less effective health outcomes.
Lean Healthcare Solution: To address this issue, Lean Healthcare adopts a patient-centered approach that emphasizes the importance of active patient participation throughout the care process. This goes beyond simply treating patients as passive recipients of healthcare services and involves them as active partners in defining perceived value and continuous improvement in care.
One of the ways in which Lean Healthcare promotes patient engagement is through the creation of open and transparent communication channels. This involves regular and effective communication between patients and healthcare professionals, where patients are encouraged to share their concerns, expectations, and relevant health information. This approach allows patients to feel heard and valued while providing essential information for informed decision-making.
Furthermore, Lean Healthcare promotes patient education, empowering them to better understand their health conditions, treatment options, and the benefits of following a care plan. This not only empowers patients to make informed decisions but also motivates them to actively engage in their own health.
Another way in which Lean Healthcare promotes patient engagement is through the establishment of feedback mechanisms, where patients can share their experiences and suggestions for improving healthcare services. This allows healthcare organizations to continuously adjust their processes and approaches to meet patient needs and expectations.
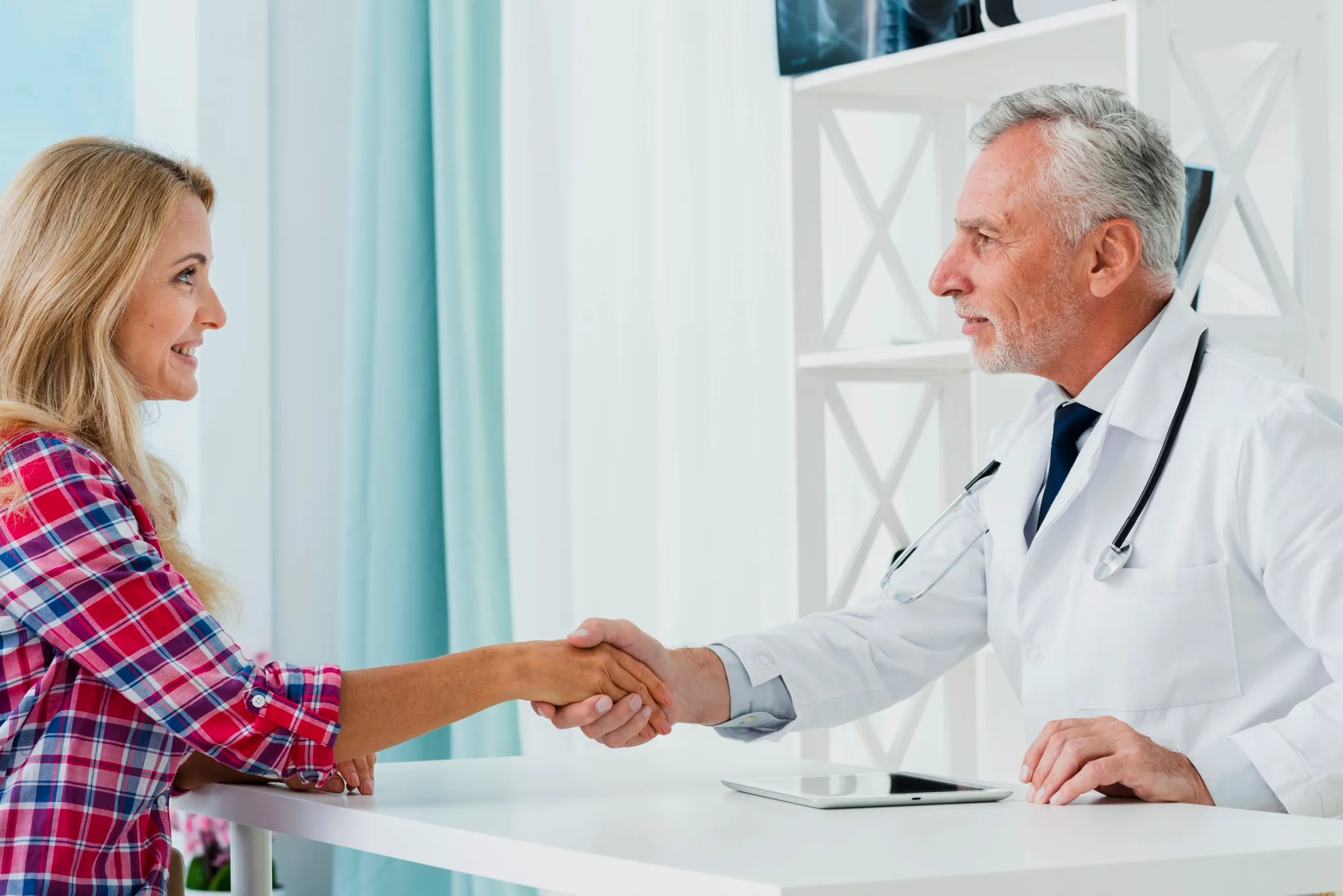
High Costs
Challenge: One of the most pressing and persistent challenges in the healthcare sector is the constant increase in costs associated with the provision of medical services. The escalating healthcare costs place significant pressures on healthcare systems, governments, insurers, and, most importantly, on the patients themselves. The rising cost of medical care can create barriers to access to care, adversely impact the quality of services, and strain the budgets of individuals and families.
Lean Healthcare Solution: Faced with this challenge, Lean Healthcare emerges as a promising strategy for reducing operational costs in the healthcare system. The Lean methodology adopts an approach based on the elimination of waste, the reduction of unnecessary inventories, and process optimization to achieve financial efficiency without compromising the quality of care.
One of the fundamental principles of Lean Healthcare is the identification and elimination of activities that do not add value to the patient. This includes unnecessary bureaucratic processes, inefficient workflows, and any expenditure that does not directly contribute to the improvement of patient health. By eliminating these wastes, healthcare organizations can reduce operational costs and redirect financial resources to areas that truly benefit patients.
Furthermore, Lean Healthcare promotes the reduction of unnecessary inventories of medical supplies and medications, avoiding excessive stockpiling that can lead to waste and increased costs. Effective inventory management not only saves money but also ensures that resources are available when and where they are needed, improving continuity of care.
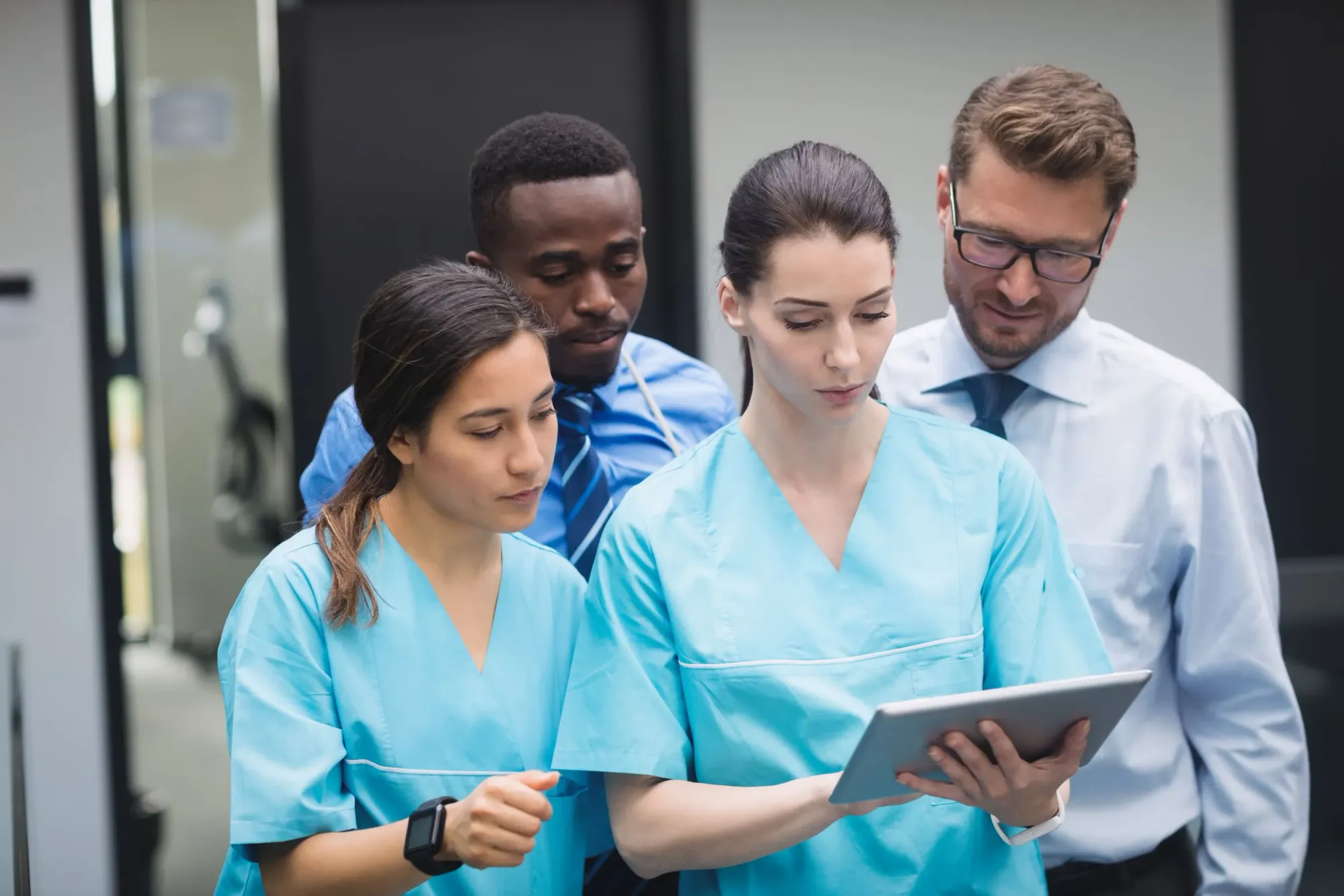
Process optimization is another crucial facet of Lean Healthcare in cost reduction. By carefully analyzing workflows and identifying bottlenecks, delays, and inefficiencies, healthcare organizations can redesign processes to be more effective and efficient. This not only saves time and resources but can also enhance the patient experience by reducing wait times and medical errors.
Medical Errors
Challenge: An extremely relevant and serious challenge in the context of healthcare is the occurrence of medical errors, which can have severe and even fatal consequences for patients. Medical errors can include misdiagnoses, improper administration of medications, poorly performed surgical procedures, and other failures that compromise the safety and effectiveness of treatments. The incidence of these errors is a constant concern for healthcare professionals, patients, and healthcare systems worldwide.
Lean Healthcare Solution: Within the scope of Lean Healthcare, mitigating the risk of medical errors is a critical priority. The Lean methodology promotes an approach centered on process standardization and continuous improvement, aiming to reduce the likelihood of errors and foster a robust culture of safety.
Process standardization is a key strategy for minimizing errors. This involves creating clear protocols and guidelines for all stages of healthcare, from patient admission to medical discharge. This standardization helps ensure that procedures are consistently performed and that best practices are followed in all cases, minimizing the margin for error.
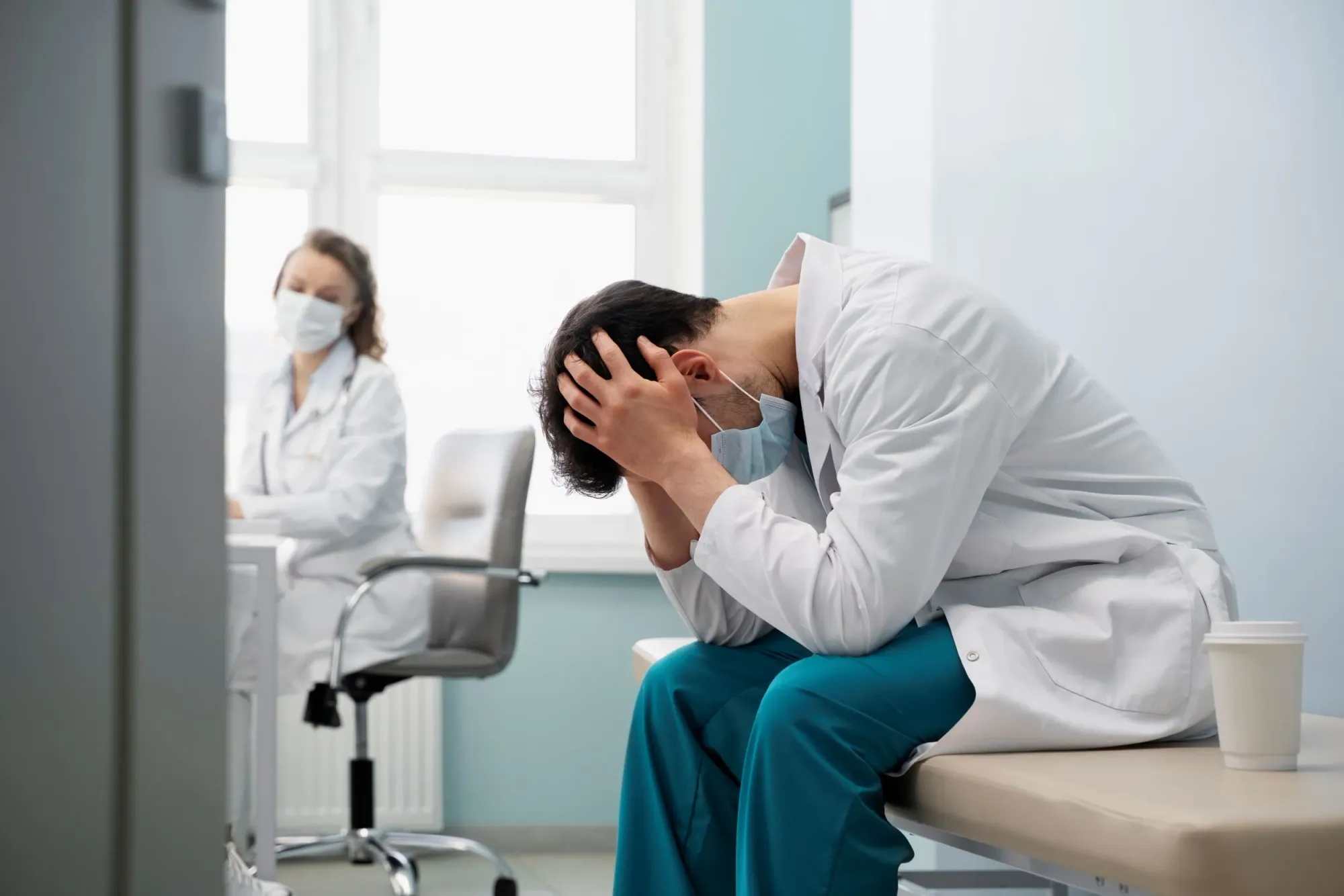
Furthermore, the Lean Healthcare methodology emphasizes the importance of continuous improvement. This means that healthcare organizations are constantly reviewing and enhancing their processes based on data and feedback. When an error occurs, instead of blaming individuals, Lean Healthcare encourages a systemic approach to understanding the underlying causes of the error and implementing corrective measures to prevent the same error from recurring.
A culture of safety is another crucial aspect of Lean Healthcare in error prevention. This involves creating an environment in which healthcare professionals feel comfortable reporting errors without fear of retaliation and where learning from mistakes is valued. By promoting a culture that prioritizes patient safety, Lean Healthcare creates an environment conducive to the proactive identification and correction of issues that could lead to medical errors.
Additionally, the use of Lean tools, such as the Cause and Effect Diagram (Ishikawa), the 5 Whys, and other root cause analysis techniques, helps identify the underlying causes of medical errors and implement effective preventive measures.
Liked the tips? Then get ready for a continuous journey of knowledge by following our blog. If you are a health professional and have not yet explored the benefits of a management software, discover the numerous advantages that Ninsaúde Clinic can provide to your clinic. Stay ahead, optimize your processes, and elevate excellence in patient care!
Image credits for cover: Freepik